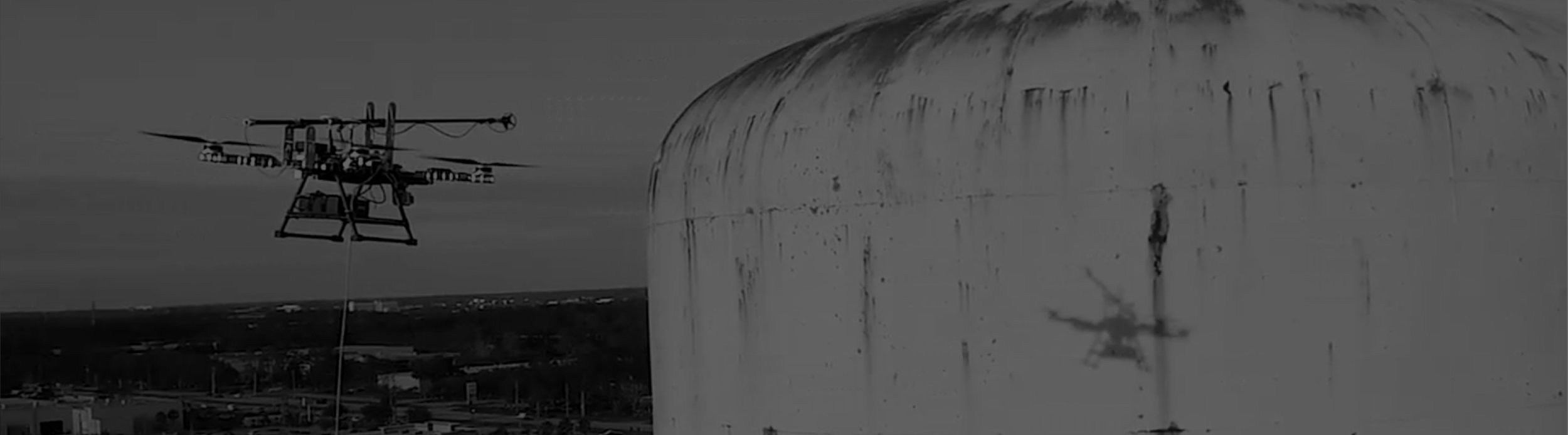
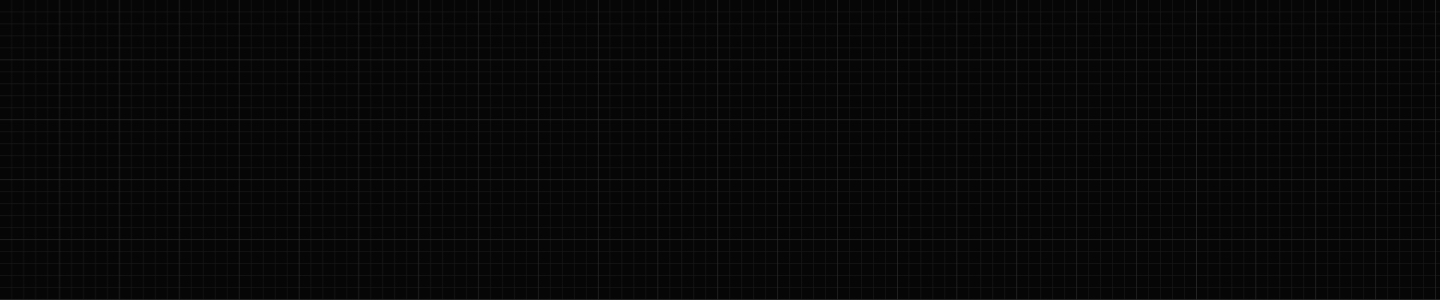
Autonomous drone for performing safe, reliable, and cost-effective ultrasonic thickness measurements at height
To learn more, read the Apellix Blog post on How Drones are Changing Corrosion Inspections in 2021 and Beyond
Interested in our services? Visit the Apellix NDT Field Services Group website
Specifications
● Performs measurements up to 100 m (330 ft) above ground level
● Over 100 separate site measures per hour, with all-day flight via ground power (no battery changes)
● Operable in winds up to 12 knots (14 mph)
● Configurable for wide temperature ranges and wall thicknesses
● Couplant applied automatically between readings
● Output includes real-time test results, customizable downloads and proprietary 3D map of test results/structure
● Requires only basic piloting skills (current US regulations require an FAA part 107 pilot license)
Uses a DeFelsko UTG M gauge with single element 5 MHz contact transducer
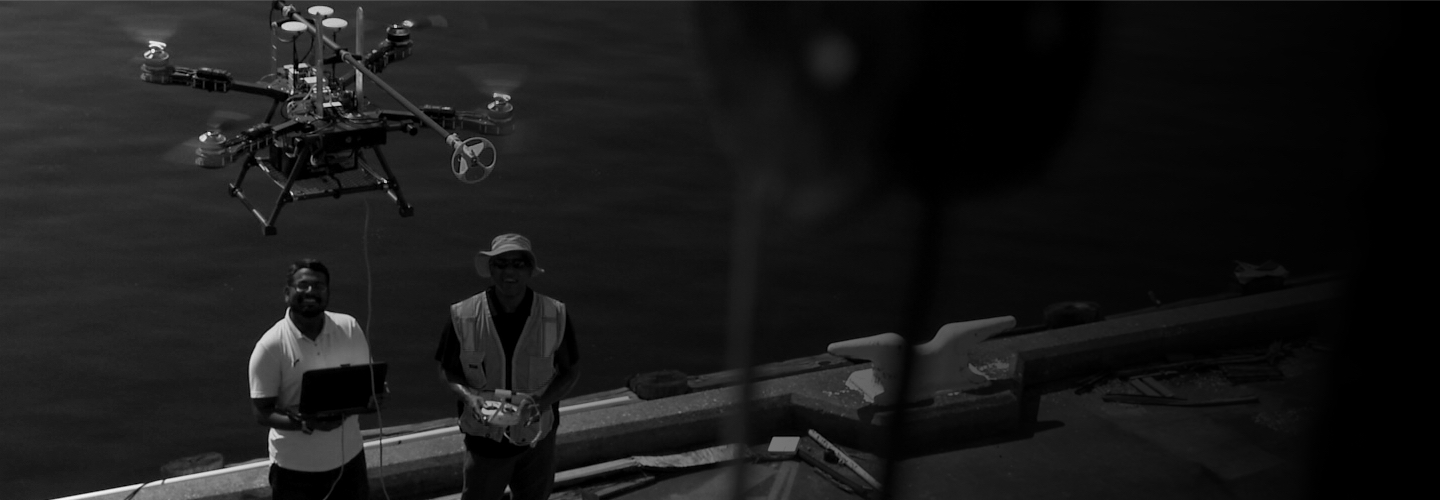
What is autonomous flight?
The pilot simply positions the aircraft near the inspection target and selects the START button on the user interface. The onboard computer then takes over, performing all flight control and testing before returning to a safe zone to await further instructions.
About Apellix Non-Destructive Testing (NDT) Robotic Devices
Our patented aerial robotic system is a hardened custom drone equipped with an array of sensor systems, a full onboard computer, and custom software to allow automatic flight to contact wall structures for measurements. The aircraft includes an articulating robotic arm with an end effector, which is the component that physically contacts the material being tested. The end effector contains the inspection measurement equipment, such as a dry film thickness or ultrasonic thickness probe. It is important to note that inspection devices measuring readings are the same technology currently used in the industry; the aerial robotic system simply places the probe against the wall surface instead of a person.
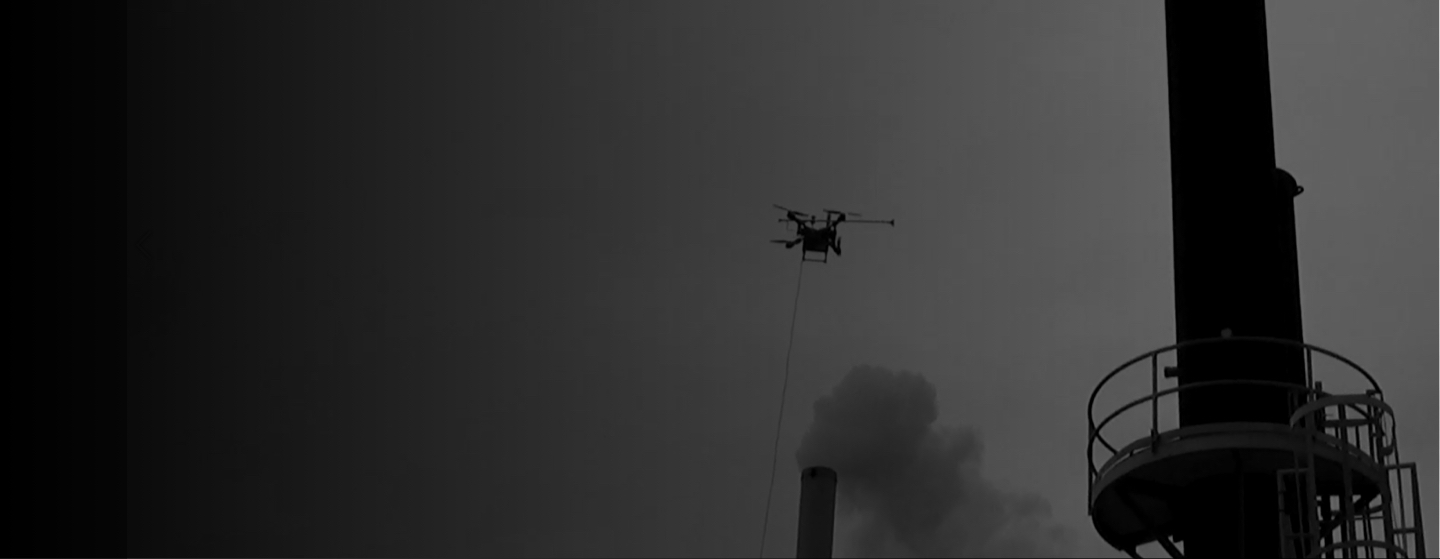
CASE STUDY
Comparison of Aerial Robotic Vs. Manual Ultrasonic
Testing on Elevated Carbon Steel Plates
Jamie L. Branch, P.E. Corrosion Engineer
This study evaluates wall thickness readings obtained using ultrasonic testing (UT) with an aerial robot and compares them with readings performed manually by a human hand. The testing surface consists of elevated carbon steel plates, constructed to approximate an above-ground storage tank.